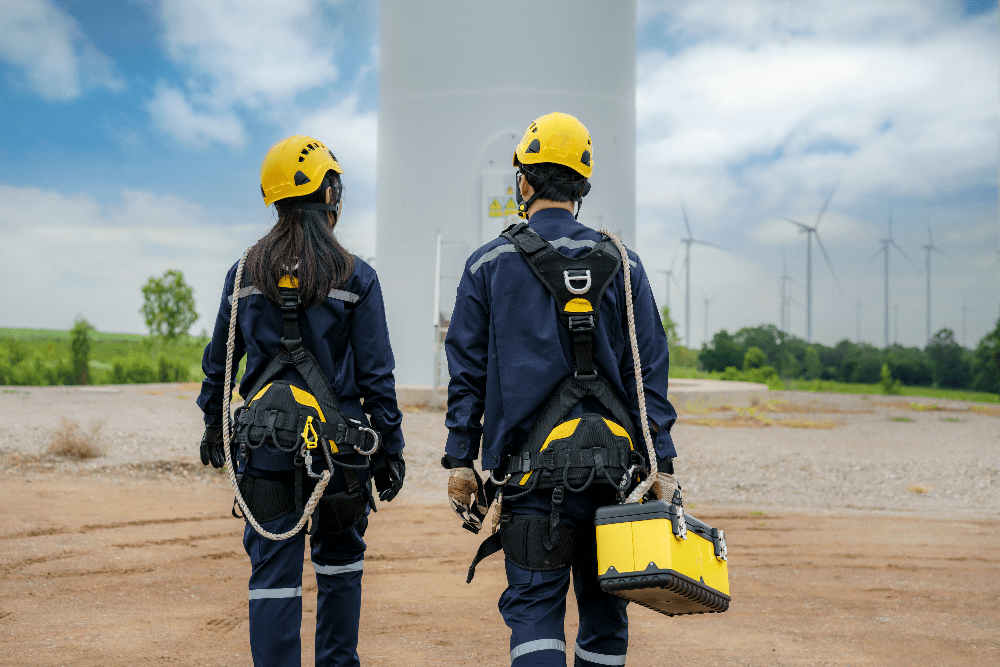
It’s clear the wind energy sector is growing fast, which means many more wind turbines will be built to meet the increasing demand. But aside from getting the turbines built, installed, and fully operational, what are the wind turbine maintenance requirements to keep them all working?
Before we dive into the detail, first, let’s take a look at the basic components of a typical wind turbine.
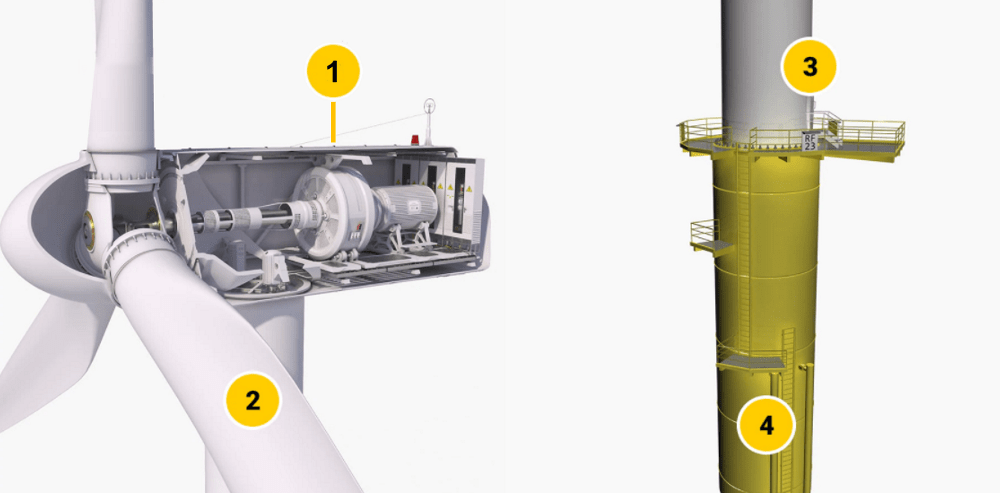
The image above shows the main sections of a wind turbine
- The Nacelle – houses the gearbox and generator
- Hub –blades are bolted in, pitched and attached to the rotor
- The Turbine Blade – catches the wind to move the rotor
- Onshore Towers – houses computer controls, power cables, built in sections and bolted together
- Offshore Towers – same as onshore, but with more complex foundations
What happens if a wind turbine is poorly maintained?
When wind turbine components fail, they can cause unscheduled stoppages, which for the operator means unscheduled service at higher rates and repair costs, potentially void the manufacturer’s warranty, not meet peak electricity demand, and lost revenue. Also, any repair or replacement of large components often requires the expensive rental of cranes and other equipment. In extreme cases, a wind turbine can catch fire, with disastrous consequences.
What parts of a wind turbine fail the most?
Many studies have looked into the reliability of wind turbine components, and although they rely on data from old turbines, there are some key trends that show where the problem areas.
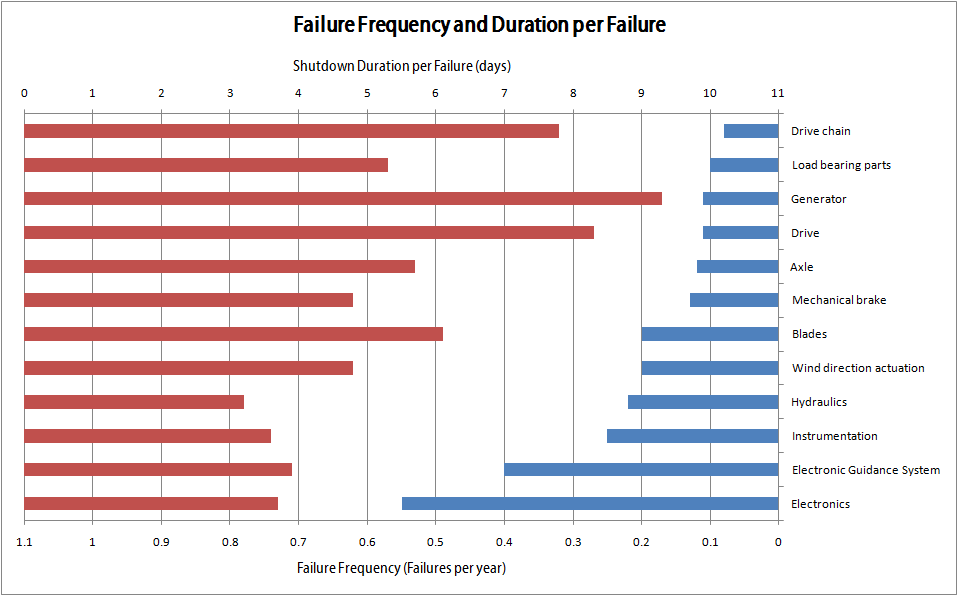
Source: Algorithmic Technologies
The statistics above on algorithmicatechnologies.com tell us that:
- At least 62.9% of all failure causes are internal engineering related failure modes while the remainder are due to external effects, mostly weather related.
- At least 69.5% of all failure consequences lead to less or no power being produced while the remainder leads to aging in some form.
- About 82.5% of all maintenance activity is hardware related and thus means that a maintenance crew must travel to the plant in order to fix the problem. This is particularly problematic when the power plant is offshore.
- On average, a failure will occur once per year for plants with less than 500 kW, twice per year for plants between 500 and 999 kW and 3.5 times per year for plants with more than 1 MW of power output. The more power producing capacity a plant has, the more often it will fail.
- The age of a plant does not lead to a significantly higher failure rate.
- The more rare the failure mode, the longer the resulting shutdown.
- A failure will, on average, lead to a shutdown lasting about 6 days.
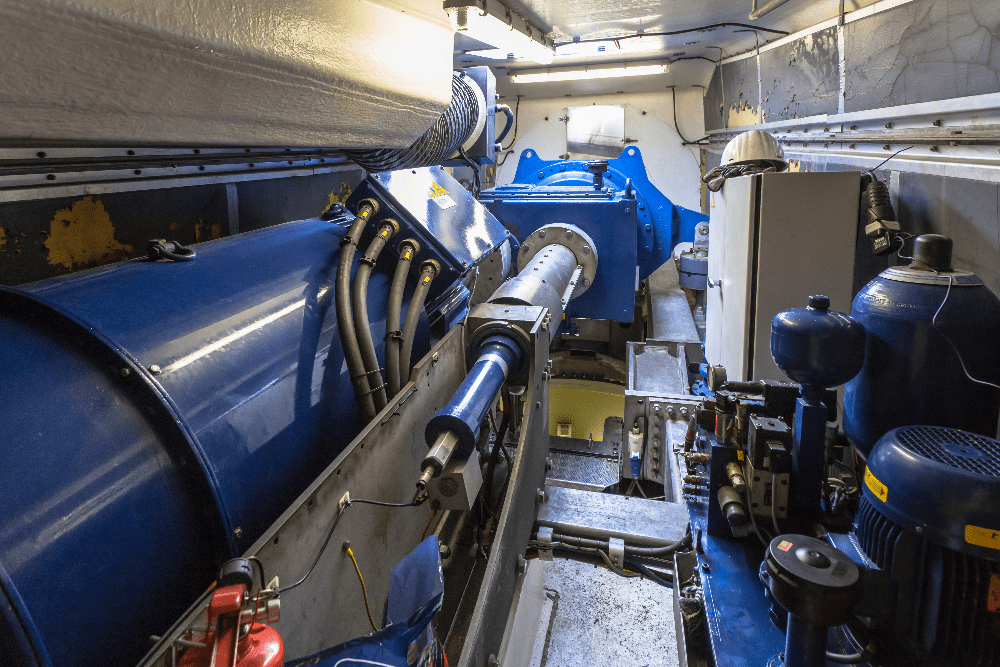
Wind Turbine Maintenance Strategies
To minimize downtime, and as part of their warranty coverage, wind farm operators adopt both preventative and predictive maintenance. Preventative Maintenance is planned maintenance to prolong the lifespan of assets. It can include adjustments, cleaning, lubrication, repairs, and replacements. Predictive Maintenance is more sophisticated and uses sensors to monitor the condition of the assets.
Maintenance check-ups typically take place a few times a year, with computerized maintenance management system software (CMMS) used to record when each turbine has been serviced. A CMMS will also automatically send notifications when a maintenance check is due.
Predictive Maintenance
Predictive maintenance for a wind turbine uses sensors placed on key components. These send valuable data back to the maintenance team to inform of lubrication levels, vibration, temperatures, and foundation displacement.
Examples of Monitoring & Predictive Maintenance
Wind turbine maintenance activities are wide-ranging, with technicians working through extensive checklists. In general, the work carried out will include :
- Inspection of the electrical cabinet, gearbox, generators, yaw system, and brake
- Assessing the blades and blade pitching
- Examining and tightening bolts
- Surveying the tower foundation
- Measuring oil and lubrication levels, sampling, and if necessary, replacing
- Alignment of the drive train
- Evaluating the nacelle
- Checking ventilation, air filters, and shock absorbers
- Repairing cracks and corrosion
- Inspecting bearing and connections
Wind Turbine Bolt Inspection
One of the most important routine maintenance activities is to perform a torque check on the bolts. A wind turbine is assembled using as many as 25,000 bolts. They are used throughout the turbine in the foundations, the tower sections, within the nacelle, and for attaching the blades to the hub.
Wind Technicians
Maintenance is done by specialist Wind Turbine Technicians, or “Windtechs” as they are known in the industry. A Windtech may work on both the construction and maintenance of wind turbines.
For obvious reasons, experienced wind technicians are in great demand. They work at heights of more than 300ft and do a large amount of work within the nacelle where most of the electronics and moving parts are housed. If you are thinking of a career change, you will need the right qualifications, a head for heights, and be comfortable working in confined spaces.
Useful Tools For Wind Turbine Technicians

There are several different types of hydraulic tools used by wind turbine technicians. These include:
- Hydraulic Torque Wrenches
- Hydraulic Bolt Tensioners
- Nut Splitters
- Tower Alignment Tools